Precision Engineering in China: Elevating Global Manufacturing with the Best Plasma Cutting Technology
In recent years, precision engineering has emerged as a cornerstone of global manufacturing excellence, with China at the forefront of this transformation. One of the key technologies driving this advancement is plasma cutting, a highly efficient and versatile method known for its ability to deliver intricate cuts and high-quality finishes in various materials. As the demand for precision components continues to rise across multiple industries—from automotive to aerospace—China is leveraging state-of-the-art plasma cutting technology to meet these challenges. This guide aims to explore the significant role of plasma cutting in enhancing manufacturing precision, its advantages over traditional cutting methods, and how Chinese manufacturers are setting new benchmarks in quality and efficiency on the global stage.
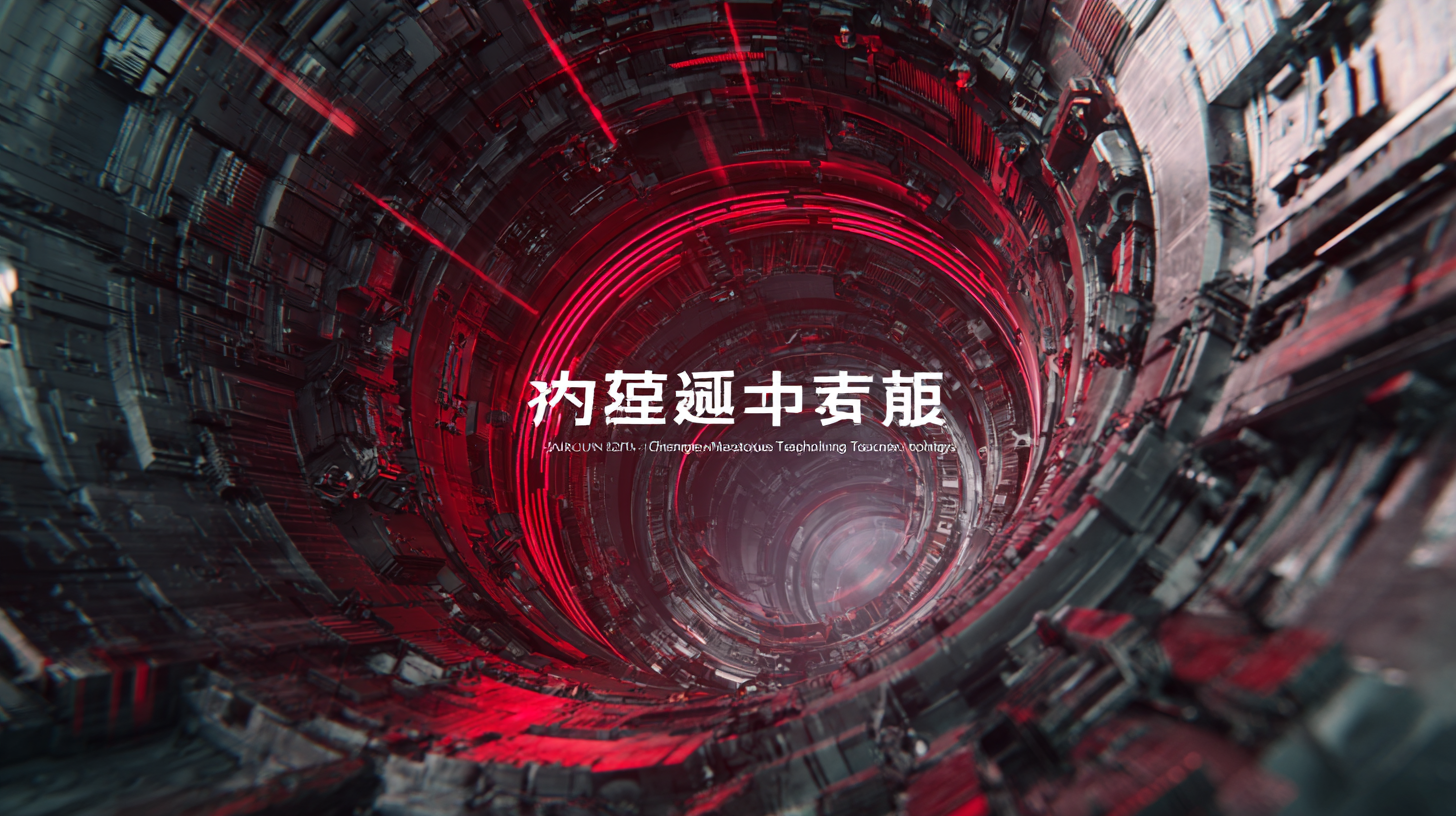
The Rise of Precision Engineering in China's Manufacturing Landscape
The rise of precision engineering in China's manufacturing landscape signifies a pivotal shift towards advanced industrial capabilities. With the Chinese government's emphasis on building a modern industrial system, it is clear that precision engineering is becoming the backbone of manufacturing practices. By championing high-quality development and integrating cutting-edge technologies such as plasma cutting, China is positioning itself as a leader in global manufacturing.
As the nation looks to enhance its industrial framework, the focus on precision engineering aligns with broader initiatives directed at modernization. The emphasis on high-end, intelligent, and green manufacturing underscores a commitment to sustainable practices while boosting production efficiency. Noteworthy investments in infrastructure, such as the ambitious transportation projects in the Pearl River Delta, further reflect this strategic move toward nurturing a sophisticated manufacturing ecosystem. This landscape not only elevates China's status but also influences global manufacturing standards through innovation and relentless pursuit of excellence.
Precision Engineering in China: Elevating Global Manufacturing with the Best Plasma Cutting Technology
Technology Type | Application Field | Advantages | Market Growth (%) | Key Regions |
---|---|---|---|---|
Plasma Cutting | Metal Fabrication | High Precision, Speed, Flexibility | 8.5% | Eastern China, Guangdong |
Laser Cutting | Aerospace, Automotive | Minimal Waste, High Accuracy | 10.2% | Beijing, Shanghai |
Water Jet Cutting | Glass, Stone | No Material Distortion | 5.7% | Northeast China |
Oxy-Fuel Cutting | Heavy Industry | Cost-Effective, Versatile | 3.9% | Northwest China |
Fiber Laser Cutting | Electronics, Medical | High Speed, Efficiency | 12.3% | Jiangsu, Zhejiang |
Understanding Plasma Cutting Technology: Principles and Applications
Plasma cutting technology has become a cornerstone in precision engineering, holding significant implications for global manufacturing. This method, which utilizes ionized gas at high temperatures to sever materials, demonstrates remarkable efficiency and precision. By enabling intricate cuts on a variety of metals, plasma cutting processes are increasingly integrated into production lines, particularly within sectors demanding high-quality outputs, like automotive and aerospace. According to recent industry reports, the global plasma cutting machine market is projected to grow significantly, with advancements in technology shaping its future.
In addition to its manufacturing applications, plasma technology has been transformative in the food processing sector. Cold plasma technology, a non-thermal method, has shown promising results in enhancing food safety and extending shelf life. Recent reviews highlight its efficacy in impacting the constituents of plant-based food products, including proteins and lipids, which are crucial for nutritional quality. Furthermore, emerging non-thermal extraction techniques, such as cold plasma, are gaining momentum for their ability to improve food preservation without compromising the integrity of the products. The adoption of these technologies not only addresses key challenges in food safety but also aligns with sustainability goals within the industry.
Comparative Analysis: Plasma Cutting vs. Traditional Cutting Methods
Plasma cutting technology has emerged as a game-changer in the manufacturing sector, particularly in China, where precision engineering is pivotal. Unlike traditional cutting methods such as flame cutting or mechanical sawing, plasma cutting utilizes a high-velocity jet of ionized gas to cut through conductive materials with remarkable accuracy. According to a recent industry report, plasma cutting can achieve tolerances of up to ±0.5 mm, significantly outperforming traditional methods which typically have tolerances around ±1.5 mm. This precision not only enhances production quality but also reduces material wastage, making it a favored choice among manufacturers worldwide.
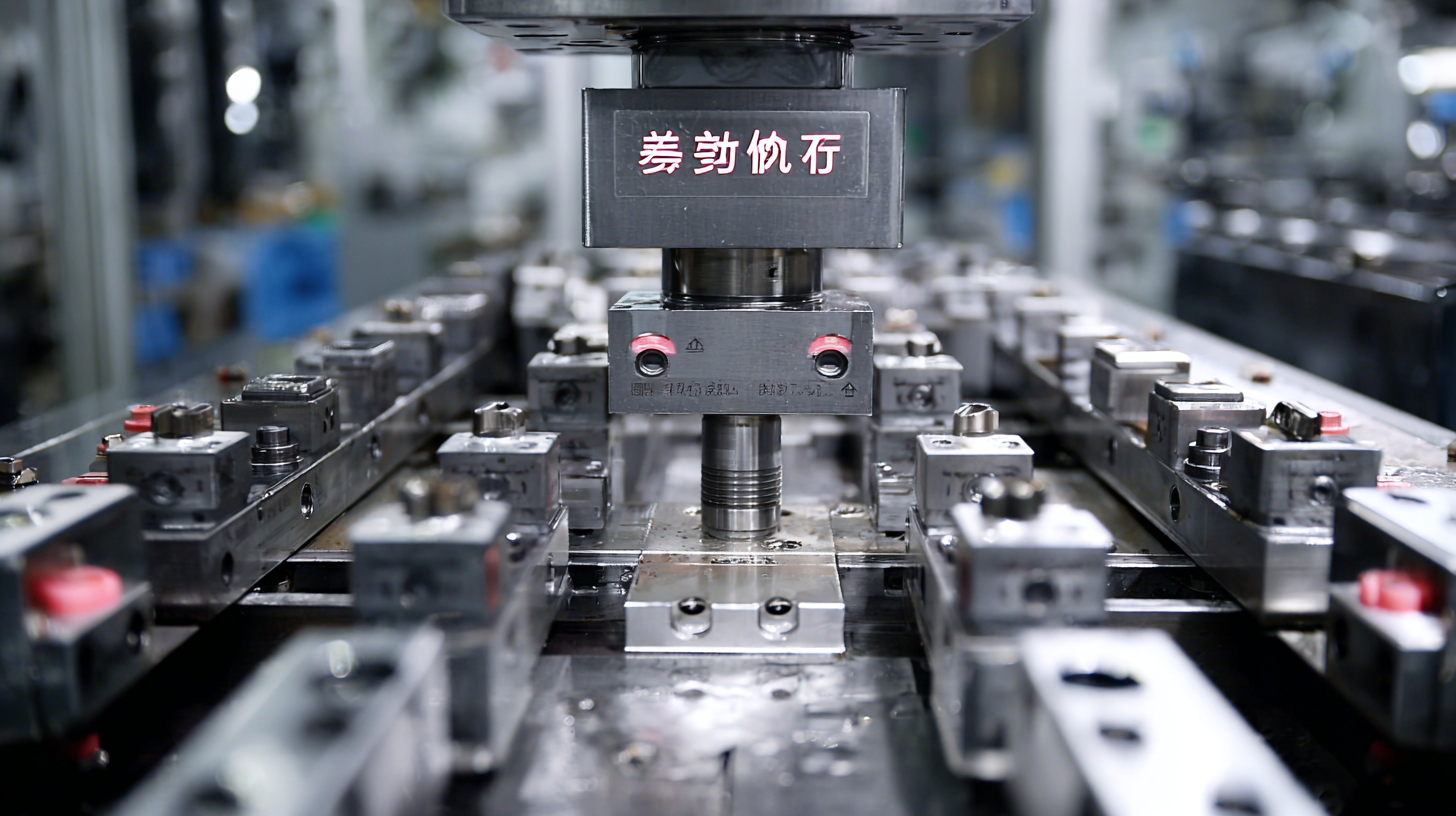
When choosing a cutting method for your projects, consider the material type and thickness. Plasma cutting excels in handling thick materials, as it can cut metal up to 300 mm thick with ease. In contrast, flame cutting is often limited to thinner substrates. Always assess your specific needs and capabilities—some manufacturers find that investing in plasma technology pays off in the long run due to increased efficiency and lower operational costs.
Tips: To maximize the advantages of plasma cutting, ensure your machinery is regularly maintained and calibrated. Also, train your operators thoroughly on safety protocols and operational best practices to avoid costly mistakes and enhance productivity. The right preparation can elevate your cutting operations and help your organization stay competitive in the fast-paced global market.
Case Studies of Successful Plasma Cutting Implementations in Industries
In recent years, precision engineering in China has witnessed significant advancements, particularly through the implementation of cutting-edge plasma cutting technology across various industries. A notable example can be seen in the automotive sector, where plasma cutting enables manufacturers to achieve intricate designs while maintaining high quality. According to a report by the International Market Analysis Research and Consulting Group, the global plasma cutting market is expected to grow at a CAGR of 5.1% from 2021 to 2026, indicating a surge in adoption driven by the need for precision and efficiency.
Another successful implementation can be found in the aerospace industry, where the lightweight and durable components produced by plasma cutting have revolutionized production processes. A case study from a leading aerospace manufacturer highlights a 25% reduction in material wastage and a 15% increase in production speed when integrating advanced plasma technology. This not only enhances operational efficiency but also reduces environmental impact, aligning with current sustainability goals.
**Tip:** When considering plasma cutting technology for your business, ensure you assess the specific needs of your production line and conduct a cost-benefit analysis to maximize efficiency gains.
**Tip:** Stay updated with the latest advancements in plasma cutting technology, as innovations such as automated systems can further optimize your production processes, leading to increased precision and reduced labor costs.
Precision Engineering in China: Plasma Cutting Technology Impact
This chart illustrates the efficiency improvements achieved through plasma cutting technology across various industries in China. The automotive and aerospace sectors show the most significant enhancements, demonstrating the impact of advanced plasma cutting technology on global manufacturing.
Future Trends: Innovations in Plasma Cutting and Precision Engineering
As the manufacturing landscape evolves, advancements in plasma cutting technology are set to play a pivotal role in precision engineering across China and beyond. The sawing and cutting tools market, valued at USD 38.2 billion in 2025, underscores a growing trend towards increased investment in precision tools and technologies. Between 2025 and 2035, the market is expected to continue its upward trajectory, reflecting the increasing demand for efficient and accurate manufacturing processes.
Moreover, the metal cutting tools market is projected to reach USD 113.04 billion by 2030, indicating a robust expansion driven by innovations in cutting technologies. The integration of Artificial Intelligence (AI) is particularly transformative, redefining the CNC machine tools market, which is anticipated to grow by USD 21.9 billion from 2025 to 2029. This environment of innovation not only enhances productivity but also supports the precision required in modern manufacturing.
Tip: To stay competitive, manufacturers should invest in the latest plasma cutting technologies that enhance accuracy and reduce waste. Incorporating AI into manufacturing processes can also improve operational efficiency, allowing for quicker adaptation to market demands. Regularly reviewing emerging technologies ensures that businesses remain at the forefront of industry advancement.
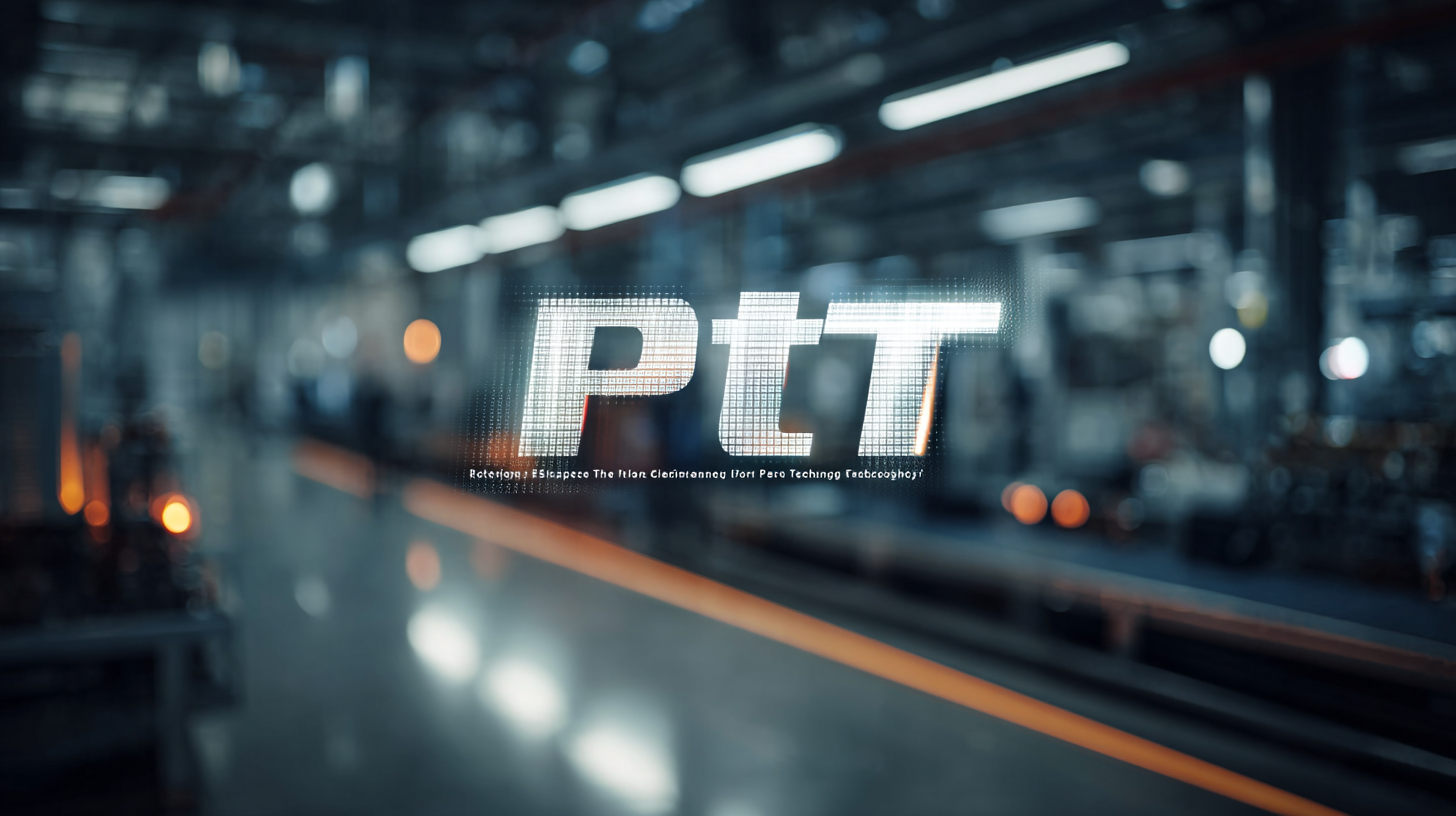