7 Reasons Why the Best Industrial Plasma Table is an Essential Investment for Global Buyers
In the rapidly evolving landscape of manufacturing, the demand for precision and efficiency has never been higher, particularly among global buyers seeking to enhance their operational capabilities. An industrial plasma table stands out as a critical investment in this context, offering cutting-edge technology that significantly boosts both production speed and accuracy. According to a report by MarketsandMarkets, the global plasma cutting equipment market is projected to grow from USD 3.1 billion in 2020 to USD 4.5 billion by 2025, reflecting an annual growth rate of more than 7%. This surge is driven by increased automation in manufacturing processes and the rising adoption of advanced cutting technologies. In this blog, we will explore seven compelling reasons why investing in the best industrial plasma table is not just beneficial, but essential for businesses aiming to stay competitive in the global marketplace.
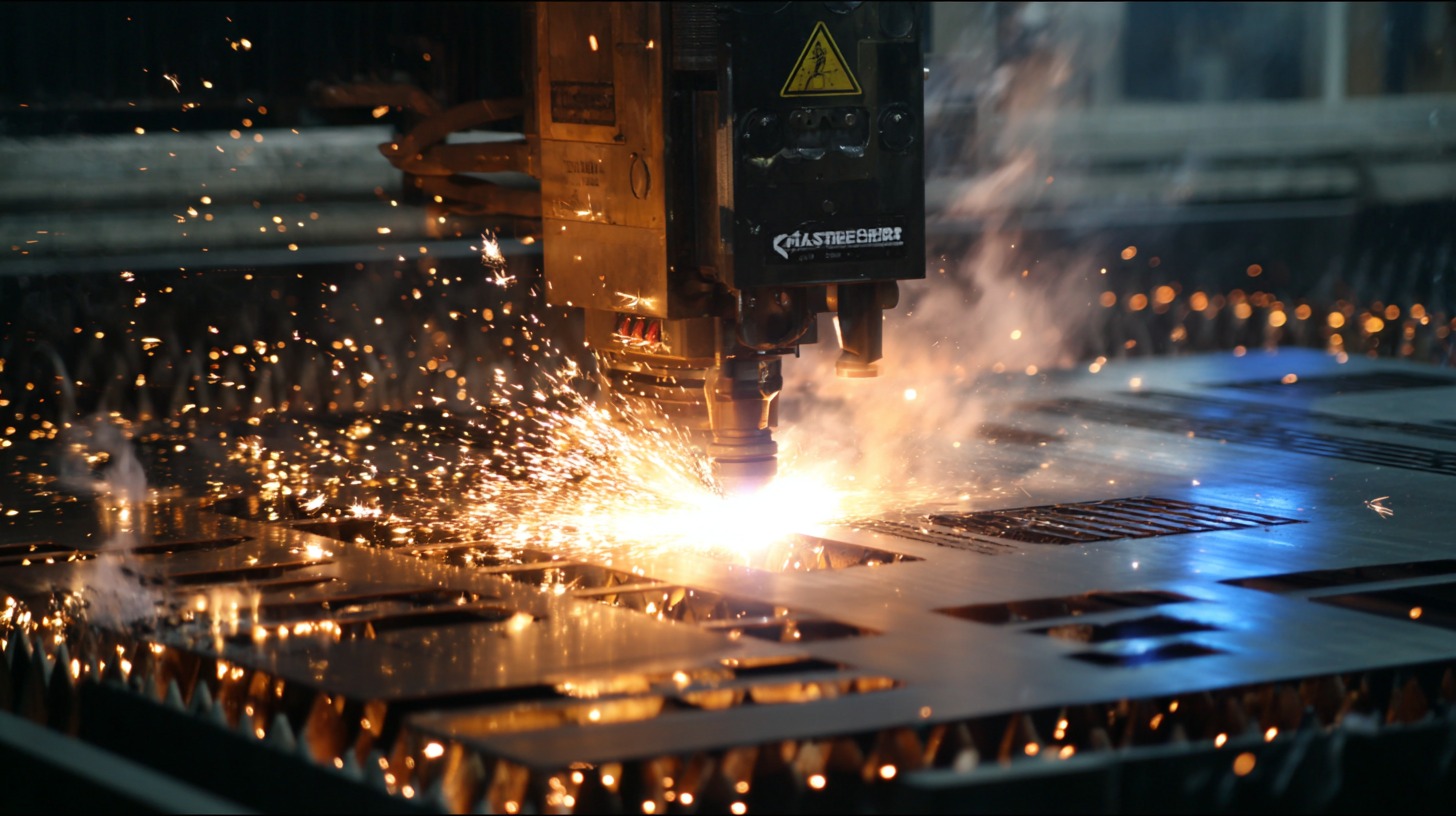
The Critical Role of Plasma Cutting in Modern Manufacturing Processes
Plasma cutting has become a cornerstone of modern manufacturing processes, offering precision and efficiency that are vital in competitive industries. According to a report by MarketsandMarkets, the global plasma cutting equipment market is expected to grow from $3.6 billion in 2020 to $5.3 billion by 2025, representing a compound annual growth rate (CAGR) of 8.2%. This growth is driven by the increasing demand for high-quality cuts and the ability of plasma technology to process a wide variety of materials quickly and accurately. Manufacturers are seeking advanced plasma table solutions that not only enhance productivity but also reduce operational costs, making them an essential investment.
The versatility of plasma cutting techniques allows for various applications, from heavy-duty metal fabrication to intricate designs in thinner materials. According to the Fabricators & Manufacturers Association, nearly 25% of all fabrication shops now utilize plasma cutting technology as part of their operations. This trend underscores the necessity for global buyers to consider investing in the best industrial plasma tables, which can provide enhanced cutting speeds and reduced scrap rates. By leveraging advancements in plasma cutting, manufacturers can optimize their workflows, ultimately leading to higher profitability and customer satisfaction in today’s fast-paced manufacturing landscape.
Key Industry Statistics Highlighting Plasma Table Efficiency and Cost-Effectiveness
In the rapidly advancing world of manufacturing, industrial plasma tables have emerged as a pivotal asset for global buyers. Recent industry statistics underscore their remarkable efficiency and cost-effectiveness. For example, plasma cutting technology can achieve speeds three to five times faster than traditional cutting methods, significantly reducing production times and increasing output. This efficiency not only boosts the productivity of operations but also allows manufacturers to respond swiftly to market demands, ultimately enhancing competitiveness.
Furthermore, the cost savings associated with plasma tables are profound. By minimizing material waste through precise cutting and reducing the overall energy consumption, these tables can lower operational costs dramatically. Industry reports indicate that manufacturers can save up to 30% on material costs alone when employing plasma technology. With advancements in automation and software integration, the investment in a top-tier plasma table becomes not just a choice but a strategic move toward achieving operational excellence and sustainability in an ever-evolving marketplace.
7 Reasons Why the Best Industrial Plasma Table is an Essential Investment for Global Buyers
Reason | Efficiency Improvement (%) | Cost Reduction (%) | Material Utilization (%) | Maintenance Cost (Annual) |
---|---|---|---|---|
Increased Cutting Speed | 30 | N/A | N/A | $2,500 |
Reduced Material Waste | N/A | 15 | 90 | $1,800 |
Versatility in Material Types | N/A | N/A | N/A | $1,200 |
Enhanced Precision | 40 | 20 | 85 | $2,000 |
Reduction in Labor Costs | N/A | 25 | N/A | $2,500 |
Longer Equipment Lifespan | N/A | N/A | N/A | $1,800 |
Environmental Benefits | N/A | N/A | 95 | $1,000 |
How Plasma Tables Enhance Precision and Reduce Material Waste in Fabrication
Plasma tables are revolutionizing the fabrication industry by significantly enhancing precision and reducing material waste. According to a report by IBISWorld, the metal fabrication market is expected to grow at an annualized rate of 3.1% over the next five years, demonstrating the increasing reliance on advanced technology such as plasma cutting. Plasma tables utilize a high-velocity jet of ionized gas to cut through metals with incredible accuracy, achieving tolerances as tight as ±0.5 mm. This level of precision not only ensures high-quality finishes but also minimizes errors that can lead to costly rework.
Moreover, the efficient use of material is a critical component in modern manufacturing. The National Association of Manufacturers (NAM) notes that material waste can account for as much as 30% of production costs in traditional fabrication processes. Plasma tables, with their advanced nesting software and cutting capabilities, can reduce this waste by up to 15%. By optimizing the layout of cuts on the material, factories can maximize their yield and reduce expenditures, making plasma tables not just a tool but a strategic investment for global buyers looking to enhance their competitiveness in an ever-tightening market.
The Impact of Advanced Plasma Technology on Production Speed and Competitiveness
In today's competitive landscape, the adoption of advanced plasma technology has become crucial for manufacturers looking to improve production speed and maintain competitiveness. According to a recent market analysis, the global plasma cutting machine market is projected to grow significantly, driven by rising demand in various applications, particularly in the automotive and aerospace sectors. The efficient cutting capabilities of plasma machines enable faster turnaround times and enhanced precision, giving companies a much-needed edge.
Investing in the best industrial plasma table not only streamlines production processes but also results in lower operational costs over time. The integration of CNC automation in plasma cutting has shown that it can increase production efficiency by up to 30%, allowing companies to meet high volumes of demand without sacrificing quality. As industries continue to recover from the impacts of COVID-19, the urgency to adopt advanced technologies becomes even more apparent.
**Tips:** When considering an investment in a plasma cutting system, evaluate the machine's compatibility with your existing production workflow. Additionally, explore options that offer flexibility in handling various materials, as versatility can significantly enhance your operational capabilities. Finally, don't overlook the importance of user training; well-trained operators can maximize the benefits of advanced plasma technology.
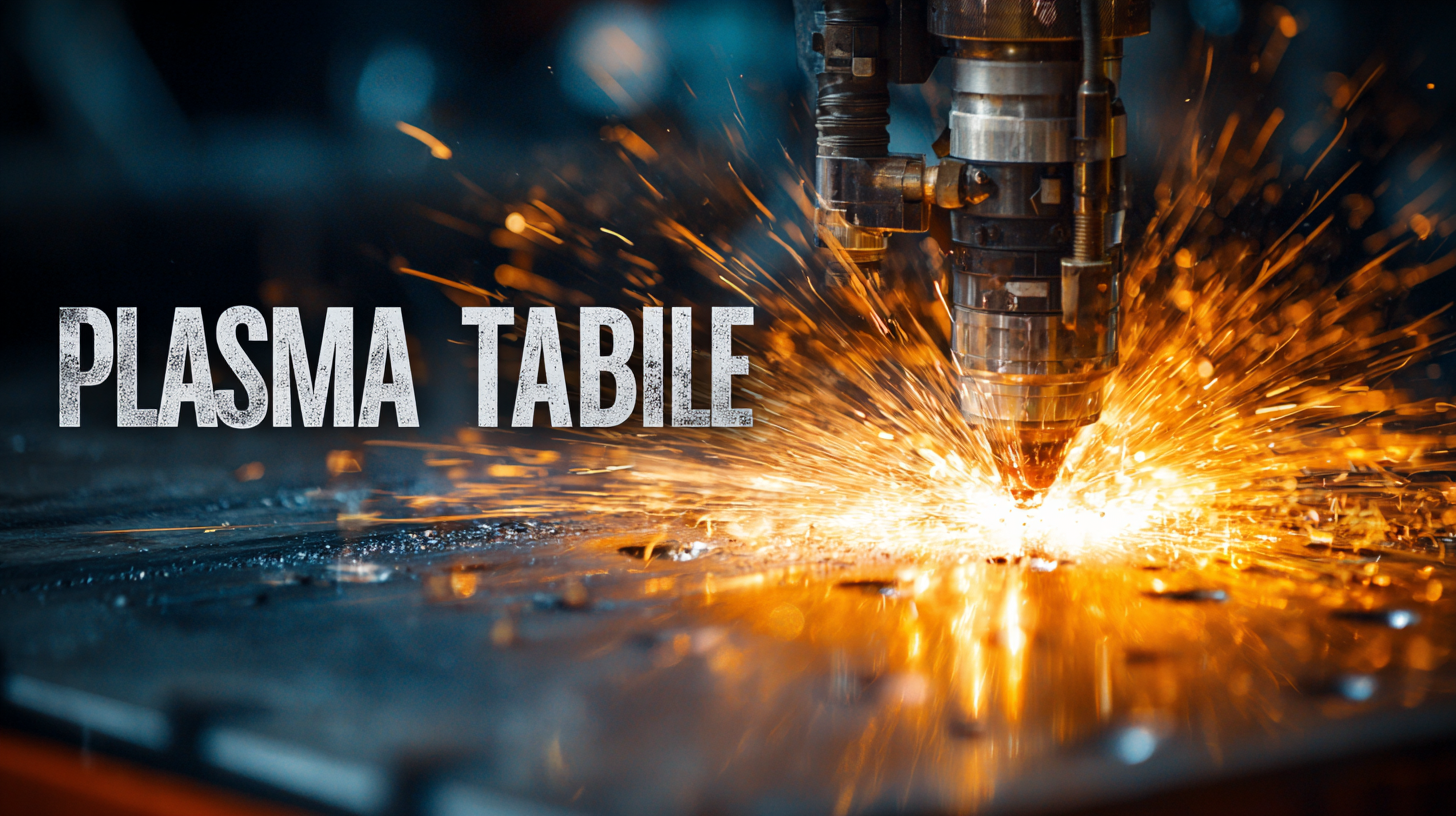
Future Trends in Plasma Cutting Technology: What Global Buyers Should Know
As plasma cutting technology evolves, global buyers must stay informed about future trends that can significantly impact their operations. The recent advancements in high-capacity cutting systems, such as the introduction of ultra-fast laser cutters, highlight the increasing demand for precision and efficiency in manufacturing. This aligns with the ongoing transitions in industries such as MedTech, where innovative medical technologies are becoming essential to address emerging health challenges. Companies that invest in advanced plasma tables are better positioned to adapt to these market shifts, ensuring they remain competitive in a landscape dominated by rapid technological advancements.
Moreover, the rise of sustainable practices in manufacturing is shaping the future of plasma cutting technology. Buyers are urged to consider equipment that not only boosts productivity but also complies with evolving environmental standards. The focus on green production in the textile and apparel industries, for instance, reflects a broader movement towards sustainability, prompting manufacturers to seek out eco-friendly production methods. By embracing new technologies that emphasize efficiency and sustainability, companies can enhance their production capabilities while contributing to a more responsible industrial landscape.
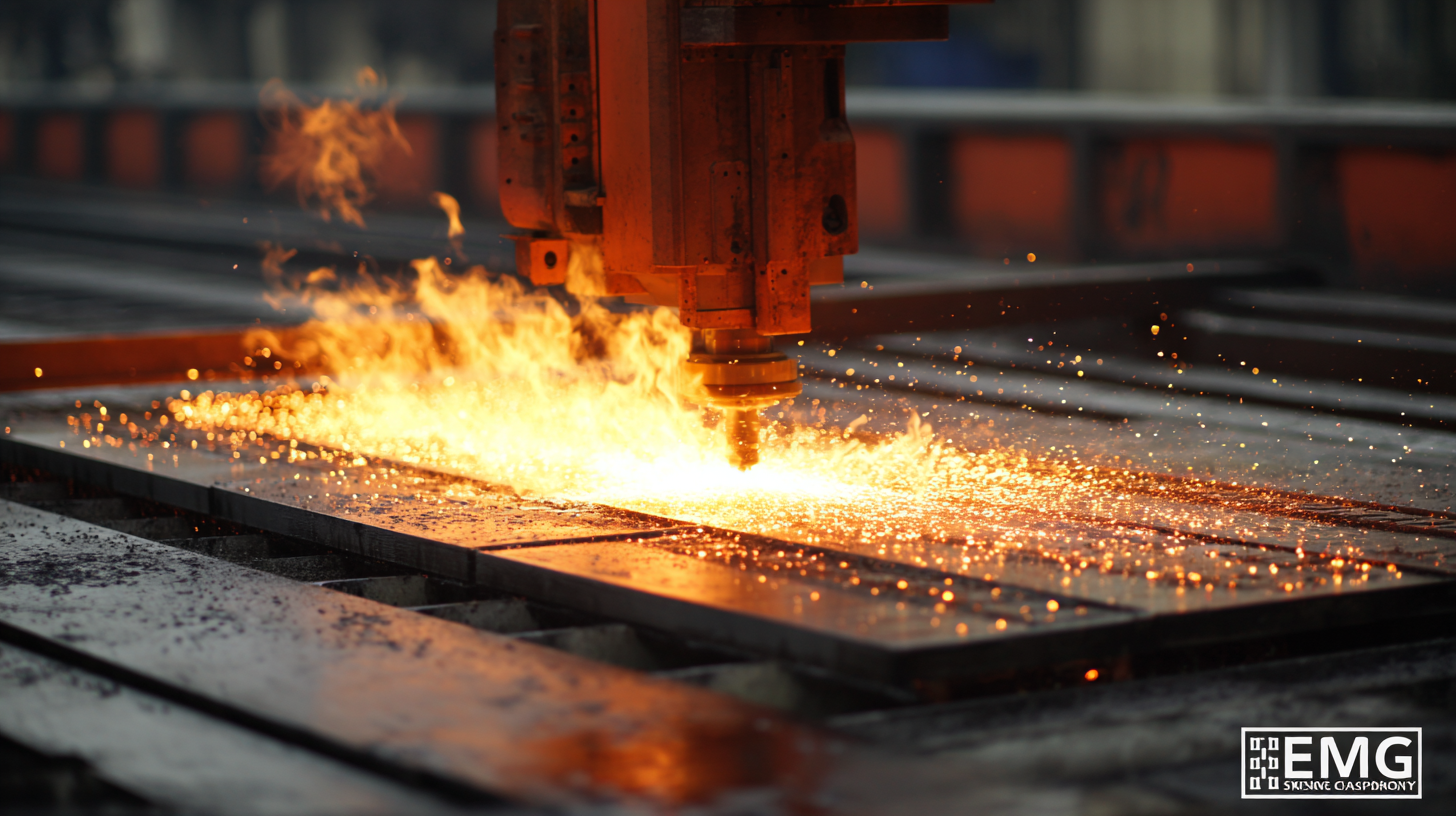